Royal Enfield
Interceptor Series II
20.08.2004 - Das neue Abdeckblech für den
Heckrahmen
kann ich
morgens in Empfang nehmen, ebenso das Stahlrohr
für meine
Standbohrmaschine. Bei
eBay USA werden zwei
Zylinderköpfe für
die Interceptor angeboten, die mir aber leider
durch die Lappen
gehen - 400 Euro plus Versandkosten sind
mir im Moment einfach
zu teuer...
21.08.2004 - Am Rahmen wird das neue Blech
angehalten und
die Befestigungslöcher angezeichnet, dann geht's erstmal ab in
den Bastelkeller. Da die bei
eBay ersteigerte Hebelblechschere
leider noch nicht an Land gekommen ist, versuche ich mein Glück
mit dem Minischleifer - klappt nicht. Also ab in den Baumarkt - und
da werde ich sogar fündig: Hauchdünne Schneidscheiben für den
kleinen Winkelschleifer versprechen leichtes Spiel mit dem harten
Material - mit Erfolg: Das Edelstahlblech schneidet sich damit
wirklich wie Butter. Nach ein paar weiteren Anpassungen des Blechs
mache ich mir Gedanken um die Befestigung der Zündspulen.
Die beste Gewichtsverteilung und Schutz vor Vibrationen scheint
mir durch liegende Befestigung der Zündspulen gegeben. In meiner
Wühlkiste finden sich 4 Gummiringe, die perfekt um die Spulen
passen, von außen soll ein abschraubbares Blech, unterstützt von
Bolzen die Spulen in die Zange nehmen. Sechskant- Bolzen aus
Edelstahl sind nicht so einfach zu bekommen, außerdem müsste
ja auch noch Gewinde geschnitten werden - ein aussichtsloses
Unterfangen bei Edelstahl. Also zurück zum Baumarkt und wieder
werde ich fündig: eine Stange Voll- Aluminium scheint dick und stabil
genug, um als Stehbolzen zu dienen. Nachdem 12 Löcher gebohrt
sind, wird ein standesgemäßes 1/4" BSF- Gewinde in die Enden der
passend gesägten Bolzenstücke geschnitten.
22.08.2004 - Das Oberflächen- Finish der
Rundstangen aus Alu
macht mir etwas Sorgen: Wieso sind da bloß so merkwürdige
Rillen drauf? Nach ein paar erfolglosen Tests mit diversen Schleif-
methoden komme ich zu dem Schluss, dass die Stücke abgedreht
werden müssen. Da ich leider keine Drehbank besitze (steht aber
schon auf der Einkaufsliste) bleibt eigentlich nur noch das Abwarten
bis zum Wochenanfang, Abgeben an eine Dreherei und Abwarten
übrig, es sei denn... Einer meiner (zugegebenermaßen seltenen)
Geistesblitze durchzuckt mich: Warum sollte nicht auch die Stand-
bohrmaschine dieser Aufgabe gewachsen sein? Ein Stück zurecht
geschliffenes Vierkanteisen dient dabei als Drehmeißel und nach ein
paar Übungen gelingt es mir, das Aluminium in mehreren Arbeits-
schritten sauber glatt zu drehen. Die restlichen Macken werden mit
der Schruppfeile und immer feiner werdendem Schleifpapier
beseitigt. Die Aktion nimmt allerdings einige Stunden in Anspruch,
besonders, weil die Bohrmaschine dem Dauereinsatz nicht ganz
gewachsen ist und nach zwei Dreh- Durchgängen eine Abkühlpause
benötigt. Wenn ich bedenke, wie viele Teile ich mittlerweile neu
gefertigt habe, kommt schon mal Neid auf die Triumph- und Norton-
Fahrer aus, die teilemäßig einfach besser dran sind.
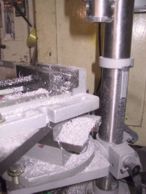 |
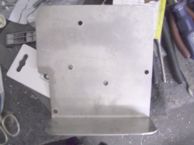 |
Meine "Drehbank" - und wo
gehobelt wird, fallen
bekanntlich auch Späne... |
Das Blech ist vorbereitet |
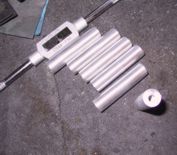 |
 |
Die Aluminium- Rundstücke |
Und so ungefähr soll das
Ganze danach aussehen |
23.08.2004 - Bevor ich überhaupt anfangen kann, müssen erstmal
die Spuren der letzten 2 Tage beseitigt werden - vor lauter Spänen
kann ich mein Werkzeug nicht mehr finden... Auf jeden Fall kann ich
endlich mal die Poliermaschine nebst den kürzlich erworbenen
Polierscheiben und -Wachsen ausprobieren. Das Arbeiten geht
mühelos, das Ergebnis an den Alu- Rundstücken kann voll
überzeugen. Ob das auch bei größeren Teilen klappt, werde ich
bei Gelegenheit an dem leicht verpfuschten Primärdeckel erproben.
Für die Alu- Rundstücke benötige ich aber wegen der Nähe zu den
Zündspulen noch ein paar Gummi- Überzüge, Schlauch würde sich
prima eignen. Da aber nichts passendes in meinem Fundus
aufzutreiben ist, werde ich morgen in der City beim Spezialisten
nachfragen.
24.08.2004 - Der Besuch beim Gummi- Spezialisten verläuft
enttäuschend - er will mir doch glatt rot-schwarz gestreiften Garten-
schlauch andrehen - ein Ansinnen, das ich entrüstet ablehne.
Im örtlichen Baumarkt werde ich beim Stöbern aber doch noch
fündig: Ein transparenter Schlauch für die Gartenbewässerung
scheint geeignet und mit einem Meter Schlauch bewaffnet kehre ich
in den heimischen Bastelkeller zurück. Nach ein paar Versuchen
gelingt es mir, den Schlauch mittels Erwärmen und Silikonfett als
Gleitmittel über die Aluteile zu schieben, so bleibt auch das schön
polierte Finish sichtbar. Als nächstes werden die Löcher für die
Alu- Stücke auf dem VA- Blech angezeichnet und gebohrt. Das
obere Abdeckblech wird aufgelegt, die nötigen Löcher angezeichnet,
vorgebohrt und nochmals angepasst. Außerdem sind der neue
Reflektor und die Boyer Powerbox (als Ersatz für Gleichrichter und
Zener- Diode) aus Frankfurt angekommen. Der neue Reflektor
ist immerhin aus Metall statt aus Plastik und macht einen deutlich
stabileren Eindruck - stammt auch von Hella. Das flache Reflektor-
glas gefällt mir an diesem aber ebenso wenig wie an dem alten
Teil, der Original Lucas Reflektor hatte ein schön gewölbtes Glas.
Er wird in dem Lampenring montiert und als letzte Tat des Tages
suche ich auf dem neuen VA- Blech nach einem geeigneten Platz
für die doch recht große Powerbox und die Boyer Zündung - das
wird langsam eng. Ordentlich Maß nehmen kann ich aber erst,
wenn ich endlich einen hinteren Kotflügel habe - der Kotflügel
sitzt direkt hinter den Komponenten.
|